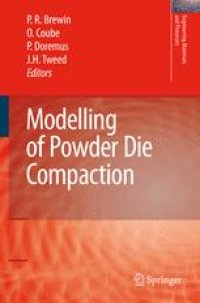
Ebook: Modelling of Powder Die Compaction
- Tags: Operating Procedures Materials Treatment, Metallic Materials, Ceramics Glass Composites Natural Methods, Structural Materials
- Series: Engineering Materials and Processes
- Year: 2008
- Publisher: Springer-Verlag London
- Edition: 1
- Language: English
- pdf
Manufacture of components from powders frequently requires a compaction step. This is widely used in powder metallurgy, ceramic, hardmetal, magnet, pharmaceutical, refractory and other sectors to make anything from complex gears for cars to pills to dishwasher tablets. Development of the tooling to manufacture a component can be a long process with several iterations. A complementary approach is to use a model of the compaction process to predict the way that powder behaves during compaction and hence the loads that need to be applied to achieve compaction and the quality of the compacted part.
Modelling of the process of die compaction has been the subject of recent collaborative research from leading experts in Europe and Modelling of Powder Die Compaction presents a summary of this state-of-the-art work, taking examples from recent world-class research. In particular, the book presents a number of case studies that have been developed to test compaction models. Full details of the data required for input to compaction models of these case studies is given, together with a survey of the techniques used to generate the data. Details are also given of methods to produce and assess components for validation of die compaction models. The inclusion of information on case studies then provides a reference for the testing and validation of compaction models.
Readers of Modelling of Powder Die Compaction will gain an appreciation of:
- The requirements in industry for models of die compaction;
- The techniques available to generate the material data required for input to compaction models;
- The production and assessment of compacts for comparison with model predictions;
- A range of compaction models and the results from exercises comparing results from these models with real powder compacts; and
- A range of potential uses and modes of use of compaction models in industry.
Manufacture of components from powders frequently requires a compaction step. This is widely used in powder metallurgy, ceramic, hardmetal, magnet, pharmaceutical, refractory and other sectors to make anything from complex gears for cars to pills to dishwasher tablets. Development of the tooling to manufacture a component can be a long process with several iterations. A complementary approach is to use a model of the compaction process to predict the way that powder behaves during compaction and hence the loads that need to be applied to achieve compaction and the quality of the compacted part.
Modelling of the process of die compaction has been the subject of recent collaborative research from leading experts in Europe and Modelling of Powder Die Compaction presents a summary of this state-of-the-art work, taking examples from recent world-class research. In particular, the book presents a number of case studies that have been developed to test compaction models. Full details of the data required for input to compaction models of these case studies is given, together with a survey of the techniques used to generate the data. Details are also given of methods to produce and assess components for validation of die compaction models. The inclusion of information on case studies then provides a reference for the testing and validation of compaction models.
Readers of Modelling of Powder Die Compaction will gain an appreciation of:
- The requirements in industry for models of die compaction;
- The techniques available to generate the material data required for input to compaction models;
- The production and assessment of compacts for comparison with model predictions;
- A range of compaction models and the results from exercises comparing results from these models with real powder compacts; and
- A range of potential uses and modes of use of compaction models in industry.
Manufacture of components from powders frequently requires a compaction step. This is widely used in powder metallurgy, ceramic, hardmetal, magnet, pharmaceutical, refractory and other sectors to make anything from complex gears for cars to pills to dishwasher tablets. Development of the tooling to manufacture a component can be a long process with several iterations. A complementary approach is to use a model of the compaction process to predict the way that powder behaves during compaction and hence the loads that need to be applied to achieve compaction and the quality of the compacted part.
Modelling of the process of die compaction has been the subject of recent collaborative research from leading experts in Europe and Modelling of Powder Die Compaction presents a summary of this state-of-the-art work, taking examples from recent world-class research. In particular, the book presents a number of case studies that have been developed to test compaction models. Full details of the data required for input to compaction models of these case studies is given, together with a survey of the techniques used to generate the data. Details are also given of methods to produce and assess components for validation of die compaction models. The inclusion of information on case studies then provides a reference for the testing and validation of compaction models.
Readers of Modelling of Powder Die Compaction will gain an appreciation of:
- The requirements in industry for models of die compaction;
- The techniques available to generate the material data required for input to compaction models;
- The production and assessment of compacts for comparison with model predictions;
- A range of compaction models and the results from exercises comparing results from these models with real powder compacts; and
- A range of potential uses and modes of use of compaction models in industry.
Content:
Front Matter....Pages i-xxi
Introduction....Pages 1-5
Modelling and Part Manufacture....Pages 7-29
Mechanics of Powder Compaction....Pages 31-42
Compaction Models....Pages 43-64
Model Input Data — Elastic Properties....Pages 65-76
Model Input Data — Plastic Properties....Pages 77-93
Model Input Data — Failure....Pages 95-103
Friction and its Measurement in Powder-Compaction Processes....Pages 105-129
Die Fill and Powder Transfer....Pages 131-150
Calibration of Compaction Models....Pages 151-163
Production of Case-study Components....Pages 165-178
Assessing Powder Compacts....Pages 179-195
Case Studies: Discussion and Guidelines....Pages 197-222
Modelling Die Compaction in the Pharmaceutical Industry....Pages 223-242
Applications in Industry....Pages 243-258
Back Matter....Pages 259-329
Manufacture of components from powders frequently requires a compaction step. This is widely used in powder metallurgy, ceramic, hardmetal, magnet, pharmaceutical, refractory and other sectors to make anything from complex gears for cars to pills to dishwasher tablets. Development of the tooling to manufacture a component can be a long process with several iterations. A complementary approach is to use a model of the compaction process to predict the way that powder behaves during compaction and hence the loads that need to be applied to achieve compaction and the quality of the compacted part.
Modelling of the process of die compaction has been the subject of recent collaborative research from leading experts in Europe and Modelling of Powder Die Compaction presents a summary of this state-of-the-art work, taking examples from recent world-class research. In particular, the book presents a number of case studies that have been developed to test compaction models. Full details of the data required for input to compaction models of these case studies is given, together with a survey of the techniques used to generate the data. Details are also given of methods to produce and assess components for validation of die compaction models. The inclusion of information on case studies then provides a reference for the testing and validation of compaction models.
Readers of Modelling of Powder Die Compaction will gain an appreciation of:
- The requirements in industry for models of die compaction;
- The techniques available to generate the material data required for input to compaction models;
- The production and assessment of compacts for comparison with model predictions;
- A range of compaction models and the results from exercises comparing results from these models with real powder compacts; and
- A range of potential uses and modes of use of compaction models in industry.
Content:
Front Matter....Pages i-xxi
Introduction....Pages 1-5
Modelling and Part Manufacture....Pages 7-29
Mechanics of Powder Compaction....Pages 31-42
Compaction Models....Pages 43-64
Model Input Data — Elastic Properties....Pages 65-76
Model Input Data — Plastic Properties....Pages 77-93
Model Input Data — Failure....Pages 95-103
Friction and its Measurement in Powder-Compaction Processes....Pages 105-129
Die Fill and Powder Transfer....Pages 131-150
Calibration of Compaction Models....Pages 151-163
Production of Case-study Components....Pages 165-178
Assessing Powder Compacts....Pages 179-195
Case Studies: Discussion and Guidelines....Pages 197-222
Modelling Die Compaction in the Pharmaceutical Industry....Pages 223-242
Applications in Industry....Pages 243-258
Back Matter....Pages 259-329
....