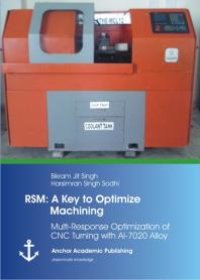
Ebook: RSM: A Key to Optimize Machining: Multi-Response Optimization of CNC Turning with Al-7020 Alloy : Multi-Response Optimization of CNC Turning with Al-7020 Alloy
Author: Bikram Jit Singh
- Tags: Experimental design -- Graphic methods., Response surfaces (Statistics) -- Germany., BUS000000, NON000000, NON000000
- Year: 2014
- Publisher: Diplomica Verlag
- City: Hamburg, GERMANY
- Edition: 1
- Language: English
- pdf
Parametric optimization, especially in machining of non-ferrous alloys seems to be quite rare and needs an immediate attention because of its associated downstream financial and non-financial losses. This book tries to fill the gap and presents an optimization problem of commonly used Al-7020 Alloy. Principles of Response Surface Methodology (RSM) have been implemented through Minitab software to bring necessary multi-response optimization, while turning on a CNC turner. The present study focuses on to enhance Material Removal Rate (MRR) while simultaneously reducing the Surface Roughness (Ra), during turning of Al-alloy. Such opposite natured response optimization is much difficult to achieve, particularly when uncoated carbide tip has been used as a cutting tool. Intensive literature survey helps to pin point parameters like; Cutting Speed, Feed Rate and Depth of Cut as a most critical to machining parameters, as far as effective and efficient optimization of selected responses are concerned. All these control-parameters are directly or inversely related to each other. If the depth of cut is increased MRR increases at the same time we get poor surface finish. Increase in the cutting speed has positive impact on both material removal rate and surface finish. Shortlisted parameters are conflicting, so we have to optimize these for further enhancement of the overall turning performance. At last, the optimized results are verified by using ANOVA as a statistical tool. This book provides quite rare Case-study of multi-response optimization (while non-ferrous CNC turning) to practioners, machinists and SME owners appropriately. Auszug aus dem Text Text Sample: Chapter: 1.1 Machining: An Introduction: Machining is a process in which a piece of raw material is cut into a desired final shape and size through a controlled material-removal activity. Traditional machining processes consist of turning, boring, drilling, milling, broaching, sawing, shaping, planning, reaming and tapping. In these ‘traditional’ or ‘conventional’ machining processes, machine tools like; lathes, milling machines, drill presses, or others, are used with a cutting tool to remove material and achieve a desired geometry (Oberg. 2004). The new technologies include; electrical discharge machining (EDM), electrochemical machining (ECM), electron beam machining (EBM), photochemical machining and ultrasonic machining etc. In current usage, the term ‘machining’ usually implies the traditional machining processes that may be performed on conventional or CNC machines. Machining is used to manufacture many metal products and further can also be used on materials such as wood, plastic, ceramic and composites. A person well versed in machining is known as a machinist. A room, building or company where machining is executed is called a machine shop. Much of modern day machining is performed out through computer numerical control (CNC), in which computers are used to monitor and control the movement or operation of the mills, lathes and other cutting machines. 1.2 Machining Operations: The major three principal machining processes are classified as turning, drilling and milling. Other operations falling into miscellaneous category include; shaping, planning, boring, broaching and sawing (Groover, 2007). Turning operations are one that rotates the work piece against the cutting tool. Lathes are the principal machine- tool used in turning. Turning is a machining process in which a cutting tool, typically a non-rotary tool bit, describes a helical tool path by moving linearly while the work piece rotates. The tool's axes of movement may be literally a straight line or they may be along some set of curves or angles, but they are essentially linear (in the non-mathematical sense). Usually the term ‘turning’ is reserved for the generation of external surfaces by cutting action, whereas this same essential cutting action when applied to internal surfaces (that is, holes, of one kind or another) is known as ‘boring’. Thus the phrase ‘turning and boring’ categorizes the larger family of (essentially similar) operations. The cutting of faces on the work piece (that is, surfaces perpendicular to its rotating axis), whether with a turning or boring tool, named as ‘facing’, and may be lumped into either category as a subset. Turning can be performed manually, in a traditional form by lathe, which frequently requires continuous supervision by the operator or by using an automated lathe, which does not. Today the most common type of such automation is computer numerical control, better known as CNC. (CNC is usually used with many other types of machining besides turning). When turning a piece of relatively rigid material (such as wood, metal, plastic or stone) is rotated and a cutting tool is traversed along axes of motion to produce precise diameters and depths. Lathes could even be used to manufacture complex geometric figures but since the advent of CNC it has become unusual to use non-computerized tool path control for this purpose. The turning operations are typically carried out on a lathe, considered to be the oldest machine tools and can be of four different types such as straight turning, taper turning, profiling or external grooving. Those types of turning processes can produce different shapes of materials such as straight, conical, curved or grooved work piece etc. In general, turning utilizes simple single-point cutting tools. Each group of work piece materials has an optimum set of tools angles which have been developed through the years. The bits of waste metal from turning operations are called ‘chips’ (in North America) or ‘swarf’ (in Britain). In some areas they may be called just ‘turnings’. Biographische Informationen PROF. BIKRAM JIT SINGH is an Associate Professor in Mechanical Department of Maharishi Markandeshwar University, Sadopur, Ambala (Haryana). He is PhD. from National Institute of Technology, Kurukshetra on Six Sigma and had done Masters of Engineering with distinction in Industrial Engineering from Thapar University, Patiala. He had a three year Professional Experience as a Manager in Light Alloy Foundry at FEDRAL MOGUL, INDIA (A US based Multi-National Company at Bahadurgarh, India.). He was undergone on the job training on SAP (PP-Module), QS-9000, ISO-TS 16949, SQC Tools and TPM for 2 years. He had worked as Lecturer in Mechanical Engineering Department for Two Years at RIMT-Institute of Engineering & Technology, Mandi Gobindgarh, India. He was also posted as HOD Mechanical at BBSBPC, Fatehgarh Sahib, India for One Year. He has around 15 International Journal publications along with paper presented in number of International and National Conferences. HARSIMRAN SINGH SODHI is working as an Assistant Professor in Department of Mechanical Engineering, Chandigarh University, Gharuan, Distt Mohali & currently doing research in the field of machining & material science. He had done post graduate in Production Engineering from Bhai Gurdas Institute of Engineering and Technology, affiliated to Punjab Technical University, Jalandhar. Presently, he has 5 years of experience in teaching. His research: Interest includes; machining, parametric optimization and metallurgy.
Download the book RSM: A Key to Optimize Machining: Multi-Response Optimization of CNC Turning with Al-7020 Alloy : Multi-Response Optimization of CNC Turning with Al-7020 Alloy for free or read online
Continue reading on any device:
Last viewed books
Related books
{related-news}
Comments (0)