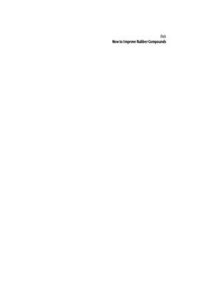
Ebook: How to Improve Rubber Compounds. 1800 Experimental Ideas for Problem Solving
Author: Dick J.S.
- Genre: Chemistry // Chemical
- Tags: Химия и химическая промышленность, Химическая технология, Технология эластомеров и изделий из них
- Language: English
- pdf
2nd Edition. — Munich: Hanser Publishers, 2013. — 407 p. — ISBN 978-1-56990-533-3The objective of this book is to provide the experienced and well-trained rubber compounder with new experimental ideas, which he or she may be able to use to improve certain specific rubber compound properties.ContentIntroduction
Complexity of Compound Ingredient Selection
Industrial Complexity
Complexity of Ingredient Property Relationships
Experimental Ideas
Sources of Ideas
Review Panel
Improving the Physical Properties of Cured Rubber Compounds
Increasing Tensile Strength
Increasing High-Temperature Tensile Strength
Increasing Ultimate Tensile Elongation
Increasing Hardness and Modulus
Reducing Set, Under Compression and/or Tension
Increasing Rebound and Decreasing Hysteresis
Increasing Tear Resistance
Increasing Hot Tear Resistance
Improving Low-Temperature Properties
Increasing Electrical Conductivity
Increasing Thermal Conductivity
Decreasing Coefficient of Friction
Decreasing Air Permeability
Increasing Rubber-to-Metal Adhesion
Improving Rubber-to-Fabric Adhesion
Improving Flame Retardance
Reducing Compound Cost
Improving Degradation Resistance of Cured Rubber Compounds
Improving Hot Air and/or Heat Aging Resistance
Improving Ozone Resistance
Improving Flex Fatigue Resistance and/or Cutting and Chipping Resistance
Improving Abrasion and/or Wear Resistance
Improving Oil and/or Solvent Resistance
Improving Staining and Discoloration Resistance
Improving Weathering Resistance
Improving Hydrolysis Resistance
Optimizing Measurable Processability Properties
Reducing Viscosity
Increasing Shear Thinning
Reducing Elasticity (Nerve)
Increasing Tack
Reducing Stickiness to Metal Surfaces
Increasing Percent Dispersion of Carbon Black and Fillers
Increasing Green Strength
Increasing Scorch Safety Time
Increasing Cure Rate
Reducing Reversion
Reducing Marching Modulus
Reducing Cold Flow
Minimizing Adverse Processing Attributes
Reducing or Eliminating Porosity, Bubbles, or Voids in Both the
Uncured and the Cured State
Mixing: Reducing Filler or Black Incorporation Times (BITs)
Mixing: Decrease Total Mixing Time
Mixing: Reducing or Eliminating Lumps in Dumped Batches
Mixing: Reducing Bagging on the Mill
Mixing: Reducing Back Rolling on the Mill
Extrusion: Reducing Die Swell (Improving Dimensional Stability)
Extrusion: Improving Smoothness of the Extrudate Surface
Extrusion: Increasing Extrusion Rate Without Loss of Quality
Calendering: Eliminating Blisters
Calendering: Improving Calender Release
Raw Material and Mixed Stock Bin Storage: Lengthening Useful Shelf Life
Mixed Stock Bin Storage: Reducing Bloom
Compression/Transfer/Injection Molding: Improving Mold Release
Compression/Transfer/Injection Molding: Reducing or Eliminating Mold Fouling
Compression/Transfer/Injection Molding: Improving Mold Flow
Compression/Transfer/Injection Molding: Reducing Shrinkage of Part
Compression/Transfer/Injection Molding: Improving Surface
Appearance
Increasing the Blow Rate During the Curing of a Sponge Compound
Eliminating Trapped Air During Molding
Reducing Backrinding
Tire Performance Properties
Improving Tire Wet Traction
Improving Tire Dry Traction
Improving Tire Winter Traction or Ice Traction
Improving Tire Rolling Resistance
Appendix 1: Blends
Introduction
SBR/NR Blends
SBR/IR Blends
SBR/BR Blends
NR/BR Blend
NR/IR Blends
NR/CIIR Blends
NR/BIIR Blends
NR/BIMS Blends
NR/IIR Blends
CR/IIR Blends
NBR/SBR Blends
NBR/PVC Blends
XNBR/PVC Blend
NBR/IR Blends
NBR/BR Blends
NBR/NR Blends
EPDM/SBR Blends
EPDM/CR Blends
EPDM/IR Blends
EPDM/NR Blends
EPDM/CSM Blends
EPDM/Silicone Compatibilized
EPDM/LDPE Blend
EPDM/EVA Blend
CR/SBR Blends
CR/BR Blends
CSM/BR Blends
CR/Hydrin Blends
NBR/FA Polysulfide Rubber
Triblends
NR/SBR/BR Blends
BR/SBR/IR Blends
NR/IR/SBR Blends
NR/EPDM/BIIR Blends
NR/EPDM/CIIR Blends
NR/CR/CSM Blends
NBR/PVC/SBR Blends
XNBR/PVC/NBR Blends
XNBR/PVC/BR Blends
XNBR/NBR/BR Blends
NBR/SBR/BR Blends
NBR/BR/NR Blends
NR/EPDM/SBR Blends
EPDM/SBR/CR Blends
Four-Way Blends
NR/EPDM/SBR/CIIR Blends
Appendix 2: Cure Systems
Introduction
General Purpose Elastomer Cure Packages
EPDM Cure Packages
NBR Cure Packages
Polychloroprene Cure Packages
General Purpose Thiourea Cure Systems for Carbon Black Loaded CR Compounds
Special Purpose Thiourea Cure Systems for Carbon Black Loaded CR Compounds
General Purpose Non-thiourea Cure Systems for Carbon Black Loaded CR Compounds
Special Purpose Non-thiourea Cure Systems for Carbon Black Loaded CR Compounds
Chlorobutyl Rubber Cure Packages
Butyl Rubber Cure Packages
Review Panel Members’ Biographies
Author’s Biography
Subject Index
Complexity of Compound Ingredient Selection
Industrial Complexity
Complexity of Ingredient Property Relationships
Experimental Ideas
Sources of Ideas
Review Panel
Improving the Physical Properties of Cured Rubber Compounds
Increasing Tensile Strength
Increasing High-Temperature Tensile Strength
Increasing Ultimate Tensile Elongation
Increasing Hardness and Modulus
Reducing Set, Under Compression and/or Tension
Increasing Rebound and Decreasing Hysteresis
Increasing Tear Resistance
Increasing Hot Tear Resistance
Improving Low-Temperature Properties
Increasing Electrical Conductivity
Increasing Thermal Conductivity
Decreasing Coefficient of Friction
Decreasing Air Permeability
Increasing Rubber-to-Metal Adhesion
Improving Rubber-to-Fabric Adhesion
Improving Flame Retardance
Reducing Compound Cost
Improving Degradation Resistance of Cured Rubber Compounds
Improving Hot Air and/or Heat Aging Resistance
Improving Ozone Resistance
Improving Flex Fatigue Resistance and/or Cutting and Chipping Resistance
Improving Abrasion and/or Wear Resistance
Improving Oil and/or Solvent Resistance
Improving Staining and Discoloration Resistance
Improving Weathering Resistance
Improving Hydrolysis Resistance
Optimizing Measurable Processability Properties
Reducing Viscosity
Increasing Shear Thinning
Reducing Elasticity (Nerve)
Increasing Tack
Reducing Stickiness to Metal Surfaces
Increasing Percent Dispersion of Carbon Black and Fillers
Increasing Green Strength
Increasing Scorch Safety Time
Increasing Cure Rate
Reducing Reversion
Reducing Marching Modulus
Reducing Cold Flow
Minimizing Adverse Processing Attributes
Reducing or Eliminating Porosity, Bubbles, or Voids in Both the
Uncured and the Cured State
Mixing: Reducing Filler or Black Incorporation Times (BITs)
Mixing: Decrease Total Mixing Time
Mixing: Reducing or Eliminating Lumps in Dumped Batches
Mixing: Reducing Bagging on the Mill
Mixing: Reducing Back Rolling on the Mill
Extrusion: Reducing Die Swell (Improving Dimensional Stability)
Extrusion: Improving Smoothness of the Extrudate Surface
Extrusion: Increasing Extrusion Rate Without Loss of Quality
Calendering: Eliminating Blisters
Calendering: Improving Calender Release
Raw Material and Mixed Stock Bin Storage: Lengthening Useful Shelf Life
Mixed Stock Bin Storage: Reducing Bloom
Compression/Transfer/Injection Molding: Improving Mold Release
Compression/Transfer/Injection Molding: Reducing or Eliminating Mold Fouling
Compression/Transfer/Injection Molding: Improving Mold Flow
Compression/Transfer/Injection Molding: Reducing Shrinkage of Part
Compression/Transfer/Injection Molding: Improving Surface
Appearance
Increasing the Blow Rate During the Curing of a Sponge Compound
Eliminating Trapped Air During Molding
Reducing Backrinding
Tire Performance Properties
Improving Tire Wet Traction
Improving Tire Dry Traction
Improving Tire Winter Traction or Ice Traction
Improving Tire Rolling Resistance
Appendix 1: Blends
Introduction
SBR/NR Blends
SBR/IR Blends
SBR/BR Blends
NR/BR Blend
NR/IR Blends
NR/CIIR Blends
NR/BIIR Blends
NR/BIMS Blends
NR/IIR Blends
CR/IIR Blends
NBR/SBR Blends
NBR/PVC Blends
XNBR/PVC Blend
NBR/IR Blends
NBR/BR Blends
NBR/NR Blends
EPDM/SBR Blends
EPDM/CR Blends
EPDM/IR Blends
EPDM/NR Blends
EPDM/CSM Blends
EPDM/Silicone Compatibilized
EPDM/LDPE Blend
EPDM/EVA Blend
CR/SBR Blends
CR/BR Blends
CSM/BR Blends
CR/Hydrin Blends
NBR/FA Polysulfide Rubber
Triblends
NR/SBR/BR Blends
BR/SBR/IR Blends
NR/IR/SBR Blends
NR/EPDM/BIIR Blends
NR/EPDM/CIIR Blends
NR/CR/CSM Blends
NBR/PVC/SBR Blends
XNBR/PVC/NBR Blends
XNBR/PVC/BR Blends
XNBR/NBR/BR Blends
NBR/SBR/BR Blends
NBR/BR/NR Blends
NR/EPDM/SBR Blends
EPDM/SBR/CR Blends
Four-Way Blends
NR/EPDM/SBR/CIIR Blends
Appendix 2: Cure Systems
Introduction
General Purpose Elastomer Cure Packages
EPDM Cure Packages
NBR Cure Packages
Polychloroprene Cure Packages
General Purpose Thiourea Cure Systems for Carbon Black Loaded CR Compounds
Special Purpose Thiourea Cure Systems for Carbon Black Loaded CR Compounds
General Purpose Non-thiourea Cure Systems for Carbon Black Loaded CR Compounds
Special Purpose Non-thiourea Cure Systems for Carbon Black Loaded CR Compounds
Chlorobutyl Rubber Cure Packages
Butyl Rubber Cure Packages
Review Panel Members’ Biographies
Author’s Biography
Subject Index
Download the book How to Improve Rubber Compounds. 1800 Experimental Ideas for Problem Solving for free or read online
Continue reading on any device:
Last viewed books
Related books
{related-news}
Comments (0)