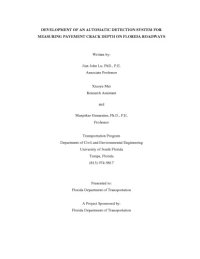
Ebook: Development of an automatic detection system for measuring pavement crack depth on Florida roadways
Author: Lu Jian John
- Tags: Pavements -- Cracking -- Florida -- Measurement, Pavements -- Florida -- Maintenance and repair
- Year: 2002
- Publisher: College of Engineering
- City: Tampa, Florida
- Language: English
- pdf
Cracking has an adverse effect on pavement performance, and hence it is an important
criterion for maintenance intervention. However, statistically reliable detection of the
extent of cracking can also be one of the major difficulties encountered when
implementing a pavement management system. The main difficulty is that there is no
reliable way to directly obtain the information on pavement crack depth without
destructing the pavement structure. This report summarizes a research project sponsored
by Florida Department of Transportation (FDOT) to develop a system that can
automatically and dynamically measure pavement cracks and estimate crack depth
without destructing the pavement structure. The principle used in the project was to use
high-accuracy laser sensors to measure the crack opening geometric including crack
width, crack edge slopes, and measurable crack depth. With these obtained data and a
neural network model developed in the project, the depth of the crack can be statistically
estimated. Based on the evaluation results, it was found that the system developed in the
project can detect pavement crack depth with a statistically reliable accuracy.
To detect crack depth, two steps are needed: crack identification and crack depth
estimation. At the early stage of the project, several approaches were proposed. These
proposed approaches included static ultrasonic method, dynamic ultrasonic sensor
method, radar sensor method, ground penetrating radar method, and so on. Based on
preliminary laboratory experiments and literature search and review, it was concluded
that these methods were not able to detect crack depth with a statistically reliable
accuracy or practical applicability. However, it was found that a combination of high-
accuracy laser sensors and estimating models could produce satisfactory results.
To dynamically identify a crack, two laser sensors were used to minimize the detection
errors. An algorithm called Partial Cross Correlation (PCC) was developed to enhance
the crack detection ability. This algorithm was evaluated through field experiments and
proven that the detection performance of PCC was much better than the approaches used
in past research studies for identifying pavement cracks.
To automatically measure the crack opening geometric, one of the key elements is the
measurement of longitudinal displacement of the measuring system. A distance sensor
was used to measure the longitudinal displacement. However, field tests found that the
sampling rate of the distance sensor had certain effect on the measurement accuracy.
Thus, a scan-rate-effect-canceling model was developed based on field experimental data
and modeling results. With the model, the accuracy of the longitudinal displacement
measurement was significantly improved.
With the obtained crack opening geometric characteristics and the information on the
pavement section such as the average daily traffic, pavement life cycle, pavement age,
and other pavement related information, a neural network model was used to estimate the
crack depth. The database used for the neural network model development was
comprised of two parts: one was the distance sensor reading including the geometric
characteristics of the crack; the other included pavement related variables. The crack
information data were obtained from 95 pavement sections with the system developed in
the project and a static ultrasonic measuring system which can statically measure crack
depth with a reliable accuracy. The pavement related information data were obtained
from a database provided by the FDOT. In the model development, different network
architectures and different training algorithms were investigated and tested. An optimal
architecture was determined based on the tests of different model architectures.
The system was implemented and installed in a manually operated push-car. This system
now can measure crack depth at a walking speed. The current system consists of two
high-accuracy laser sensors, a longitudinal distance measuring sensor, a portable
computer with an interface to communicate with the sensors, and a comprehensive model
software used to estimate pavement crack depth using the readings from these sensors
and the pavement section related information. The system can only be used to measure
transverse crack depth since the developed neural network model was based on field data
of transverse cracks. To measure longitudinal crack depth, longitudinal crack data are
needed for modeling purpose.
Although the system is now operated at walking speed, it can be operated in a much
faster speed close to 55 mph if adequate modifications are implemented to increase the
sampling interval and the sampling rate by using a more powerful computer such as an
industry computer.
criterion for maintenance intervention. However, statistically reliable detection of the
extent of cracking can also be one of the major difficulties encountered when
implementing a pavement management system. The main difficulty is that there is no
reliable way to directly obtain the information on pavement crack depth without
destructing the pavement structure. This report summarizes a research project sponsored
by Florida Department of Transportation (FDOT) to develop a system that can
automatically and dynamically measure pavement cracks and estimate crack depth
without destructing the pavement structure. The principle used in the project was to use
high-accuracy laser sensors to measure the crack opening geometric including crack
width, crack edge slopes, and measurable crack depth. With these obtained data and a
neural network model developed in the project, the depth of the crack can be statistically
estimated. Based on the evaluation results, it was found that the system developed in the
project can detect pavement crack depth with a statistically reliable accuracy.
To detect crack depth, two steps are needed: crack identification and crack depth
estimation. At the early stage of the project, several approaches were proposed. These
proposed approaches included static ultrasonic method, dynamic ultrasonic sensor
method, radar sensor method, ground penetrating radar method, and so on. Based on
preliminary laboratory experiments and literature search and review, it was concluded
that these methods were not able to detect crack depth with a statistically reliable
accuracy or practical applicability. However, it was found that a combination of high-
accuracy laser sensors and estimating models could produce satisfactory results.
To dynamically identify a crack, two laser sensors were used to minimize the detection
errors. An algorithm called Partial Cross Correlation (PCC) was developed to enhance
the crack detection ability. This algorithm was evaluated through field experiments and
proven that the detection performance of PCC was much better than the approaches used
in past research studies for identifying pavement cracks.
To automatically measure the crack opening geometric, one of the key elements is the
measurement of longitudinal displacement of the measuring system. A distance sensor
was used to measure the longitudinal displacement. However, field tests found that the
sampling rate of the distance sensor had certain effect on the measurement accuracy.
Thus, a scan-rate-effect-canceling model was developed based on field experimental data
and modeling results. With the model, the accuracy of the longitudinal displacement
measurement was significantly improved.
With the obtained crack opening geometric characteristics and the information on the
pavement section such as the average daily traffic, pavement life cycle, pavement age,
and other pavement related information, a neural network model was used to estimate the
crack depth. The database used for the neural network model development was
comprised of two parts: one was the distance sensor reading including the geometric
characteristics of the crack; the other included pavement related variables. The crack
information data were obtained from 95 pavement sections with the system developed in
the project and a static ultrasonic measuring system which can statically measure crack
depth with a reliable accuracy. The pavement related information data were obtained
from a database provided by the FDOT. In the model development, different network
architectures and different training algorithms were investigated and tested. An optimal
architecture was determined based on the tests of different model architectures.
The system was implemented and installed in a manually operated push-car. This system
now can measure crack depth at a walking speed. The current system consists of two
high-accuracy laser sensors, a longitudinal distance measuring sensor, a portable
computer with an interface to communicate with the sensors, and a comprehensive model
software used to estimate pavement crack depth using the readings from these sensors
and the pavement section related information. The system can only be used to measure
transverse crack depth since the developed neural network model was based on field data
of transverse cracks. To measure longitudinal crack depth, longitudinal crack data are
needed for modeling purpose.
Although the system is now operated at walking speed, it can be operated in a much
faster speed close to 55 mph if adequate modifications are implemented to increase the
sampling interval and the sampling rate by using a more powerful computer such as an
industry computer.
Download the book Development of an automatic detection system for measuring pavement crack depth on Florida roadways for free or read online
Continue reading on any device:
Last viewed books
Related books
{related-news}
Comments (0)